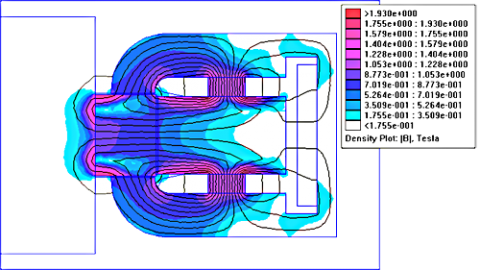
Calnetix Technologies' engineering team is committed to a comprehensive design process that balances magnetic, thermal and structural factors to ensure an optimal design solution.
To stay the best, Calnetix makes a significant investment in research and development activities every year that far exceeds industry standards.
Calnetix offers in-house analysis capabilities and a vast array of designs, which include the following:
Calnetix Technologies utilizes both closed-form mathematical modeling and finite element method modeling for electromagnetic analysis. For motor generator designs, closed form computer models developed at Calnetix, based on permanent magnet synchronous machine theory, provide fast and accurate tradeoff studies of machine parameters, such as number of poles, stator configuration, material selection, machine aspect ratios, etc. Magnetic Bearing design and analysis software is based on a unique proprietary approach taking advantage of both analytical closed-form modeling and finite element analysis working in tandem in order to generate an optimal electromagnetic design and accurately predict its performance parameters. The finite element method is utilized in conjunction with the closed form method to provide design optimization and to accurately calculate magnetic flux leakage that is essential for accurate machine performance prediction in both motor generator and magnetic bearing systems.
Calnetix utilizes Solidworks as a software-based platform for mechanical design. Complete systems can be modeled in this 3D design package to ensure optimum mechanical integration of this high-performance technology. During the design process, the customer approves interface control drawings to ensure that the designed system meets all mechanical interface requirements. Designs are validated in supporting analysis; upon completion, the design is released and fabricated per ISO9001 requirements.
Calnetix offers complete rotordynamic analysis using in-house-developed, finite-element-based rotordynamic analysis tools for motor generators and magnetic bearing systems (MBS). For motor generators, this analysis determines critical rotor characteristics for high-speed performance; these characteristics are either passed onto the customer for use in system integration or used internally for modeling of a Calnetix-designed system (including customer specified bearings, rotor components and structural support). For magnetic bearing systems, this approach allows coupling of the MBS control equations to the rotor and housing structural models for complete system analysis. This rotordynamic analysis allows the overall system design to be optimized for bearing and position sensor location.
MBS analysis includes:
This analysis provides the basis for the controller compensation algorithm that is used to levitate the system.
Modern high speed turbomachinery presents unique design challenges. Most businesses have not developed this expertise internally. As part of high-speed rotating machinery development programs, Calnetix Technologies provides the necessary experience, process, and attention to detail for correct integration of components into a complex machine. Experienced design and analysis engineers work together with state of the art modeling and stress analysis tools. This includes modeling the rotating and structural components for design loads, overloads, modal analysis and heat transfer, as needed. The final design is a machine that meets all life requirements.
Calnetix Magnetic Bearing Controllers and Motor Drives employ embedded controls to perform dedicated control functions specific to Calnetix designed motor generator and bearing performance needs. Calnetix develops its own embedded hardware and associated software to address the needs of complex electrical, mechanical and system design and integration requirements. Calnetix employs two development platforms based on the Texas Instruments (TI) DSP and the Motorola Freescale DSP for its magnetic bearing controllers and motor drives. These embedded controllers feature high speed DSP, PWM drives, analog and digital I/Os, and on-board flash and RAM. The user can control and monitor the embedded controllers by using Modbus through RS485/232, or digital/analog I/Os. Ethernet or USB port interfaces are also available.
To take full advantage of the latest technology in motor generators, Calnetix Technologies utilizes the latest technology in motor drives and inverters. Whether developing, integrating or manufacturing the necessary power electronics, Calnetix always designs with the system and application in mind. Currently, Calnetix utilizes both sensor-based and sensorless motor drive technology based on the needs of the system. A few of the products Calnetix has delivered include:
Our Sine Wave drives utilize space vector controls with interleaving switching to reduce the current harmonics in the motor. Motors are designed with these harmonics in mind to ensure that the system will operate at peak performance. For power generation, Calnetix has delivered both generators and inverters for stand-alone and grid-tie applications. Besides the existing line of drives and inverters, Calnetix designs and manufactures custom electronics for niche applications in various industries. Calnetix’s in-depth understanding of electromechanical, electromagnetic and electronic systems results in robust products utilized in industrial, aerospace and military applications globally.
Calnetix Technologies employs a comprehensive six-stage product development process to manage our customer system integration projects. Each project is unique and requires individual attention to estimate the project timeline and schedule. In the spirit of continuous improvement, following a project’s completion, the project team meets to review the entire process and evaluate the product for ways to enhance the value delivered. Customers are encouraged to and often participate in the development review meetings.
Phase 1
Phase 2
Phase 3
Phase 4
Phase 5
Phase 6
The concept design work is conducted based on the initial requirements from the customer and is completed within an agreed upon time frame. In this phase, design tradeoffs are typically conducted to come up with best possible design concept for the application. Performance and cost estimates, risk assessments and a compliance matrix are then prepared and presented to the customer for consideration. In addition, the initial project’s development plan including the scope of work split (engineering, hardware and integration), design verification testing plan, major project milestones, deliverables and project schedule are updated and discussed with customer in a concept design review meeting.